How to jumpstart digital transformation in manufacturing
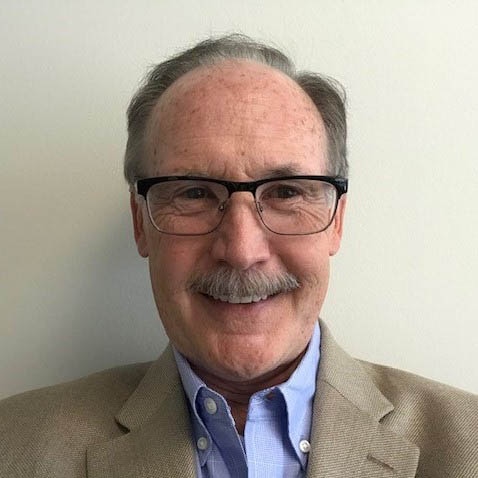
Industry 4.0 has been a significant spur toward the digital transformation of the manufacturing sector. The main objectives of Industry 4.0 are to implement technological advances and improved connectivity to help streamline manufacturing processes, drive productivity and increase cost efficiencies. This trend was already gaining steam and has gained additional impetus driven by the ever-increasing amount of data and data analytics available, and more easily accessible than ever before due to leaps in connectivity. Additionally, digital transformation became almost imperative after manufacturers saw production and supply chains thrown into an uproar by the disruptive trends of a worldwide health crisis.
While facing the challenges of upgrading their networks and technology, manufacturing executives also face the daunting prospect of retaining top talent and attracting new workers in a historically tight labor market. Simply put, to compensate for impacts on supply chains, material costs and labor shortages. manufacturers must keep pushing for more innovation, growth and agility through digital modernization.
According to SupplyChainBrain, “The idea behind Industry 4.0 innovations for manufacturing is to take existing automation processes and strengthen them with such tools as the internet of things (IoT), machine learning, augmented reality and cloud and edge computing, among others. By tapping these new technologies, manufacturers increase cross-team visibility, functionality and, ultimately, their bottom lines.”
The 2022 Marcum National Manufacturing Survey Report suggests that “with a continued labor shortage and an aging workforce, hiring, recruiting and retention will look different than ever before for manufacturers." The report concludes that “using technology to drive efficiency, innovation and address worker shortages is key for manufacturers.”
Industry 4.0 has already had a significant impact. The digital transformation that must accompany a 4.0 approach presents opportunities for manufacturers to improve operations and competitiveness. McKinsey & Company explains, “Companies at the front of the pack are capturing benefits across the entire manufacturing value chain — increasing production capacity and reducing material losses, improving customer service and delivery lead times, achieving higher employee satisfaction, and reducing their environmental impact. Scaled across networks, these gains can fundamentally transform a company’s competitive position.”
The first step is a big one
Right now, worldwide, manufacturers are experiencing one of the largest shifts in technology since the Industrial Revolution. The judicious use of new technologies and solutions can fundamentally improve a manufacturer’s standing in the industry if the adoption of new processes is accomplished in a well-planned and strategic manner. Digital transformation can be challenging to implement, though — and many manufacturers are falling behind on the digital transformation curve.
Manufacturers may find it almost impossible to achieve the benefits of Industry 4.0 while relying on an aging network infrastructure. What’s needed to take the first steps of the 4.0 journey is a modernized network. It’s a big leap to take, especially considering that manufacturers often keep legacy systems running for longer than a decade, but that approach is simply not viable anymore. Unfortunately, legacy connectivity between sites and data centers may not be suited to support digital transformation projects for manufacturers. Further, those organizations that have not invested in software-defined networking solutions may experience latency and security issues.
Digital transformation supported by a modernized network is key
Factories seeking future growth and success will need a scalable, ultra-high speed, high-bandwidth infrastructure solution. They should be building diverse, resilient, secure infrastructure paths between geographically distributed facilities, cloud and data center environments. Infrastructure solutions exist today that enable manufacturers to adopt new technology, add services as needs evolve, or migrate to newer technologies, when necessary, without having to worry about outdated infrastructure.
The benefits are clear, considering the sort of data crunching and analysis that can be accomplished with today’s technology based on a modernized network. Manufacturers can gain actionable insight from data and analytics, AI and digitally enabled machinery and processes. This can result in opportunities to add significant value to their companies and give them a competitive edge. McKinsey estimates that companies could see forecasting accuracy increases of up to 85%, machine downtime reductions of 30 to 50%, throughput increases of 10 to 30% and labor productivity improvements ranging from 15 to 30%.
Why are CEOs on board for digital transformation?
According to Gartner, the top four objectives companies hope to achieve by investing in emerging technology solutions are:
- Improve employee productivity
- Improve existing products or services
- Automate business processes
- Improve competitive differentiation
A lot of key folks in the manufacturing sector may not only be thinking along those lines but are investing in those outcomes. DeLoitte reports that 76% of U.S. manufacturing executives intend to increase their investments in digital initiatives and pilot more Industry 4.0 technologies.
Further, Gartner reports that 64% of IT executives see the current talent shortage as a barrier to adopting emerging technologies. It might behoove those executives to investigate managed, or co-managed, solutions from a trusted partner.
How Spectrum Business can help
Spectrum Business has developed solutions that can ease manufacturers’ entry into their digital transformation journey and their embracing of Industry 4.0. For example, our Managed Workplace Package includes Unified Communications with RingCentral and brings together connectivity, networking, security, equipment and more into a single solution. The intuitive, cloud-based portal makes operating a manufacturing network easier than manufacturers may expect. Manufacturers can choose from fully or co-managed managed services — including planning, installation and operation backed by 24/7/365, U.S.-based support.
Spectrum Business delivers technology solutions to 80% of Fortune 500 manufacturing companies. See why they do and learn more about the Managed Workplace Package.
Keep up on the latest
Sign up now to get additional stories on connectivity, security and more.
Forms cannot be submitted at this time. Please call to speak with a representative.