How SmartCap’s AI-enabled smart factory achieved recognition and success
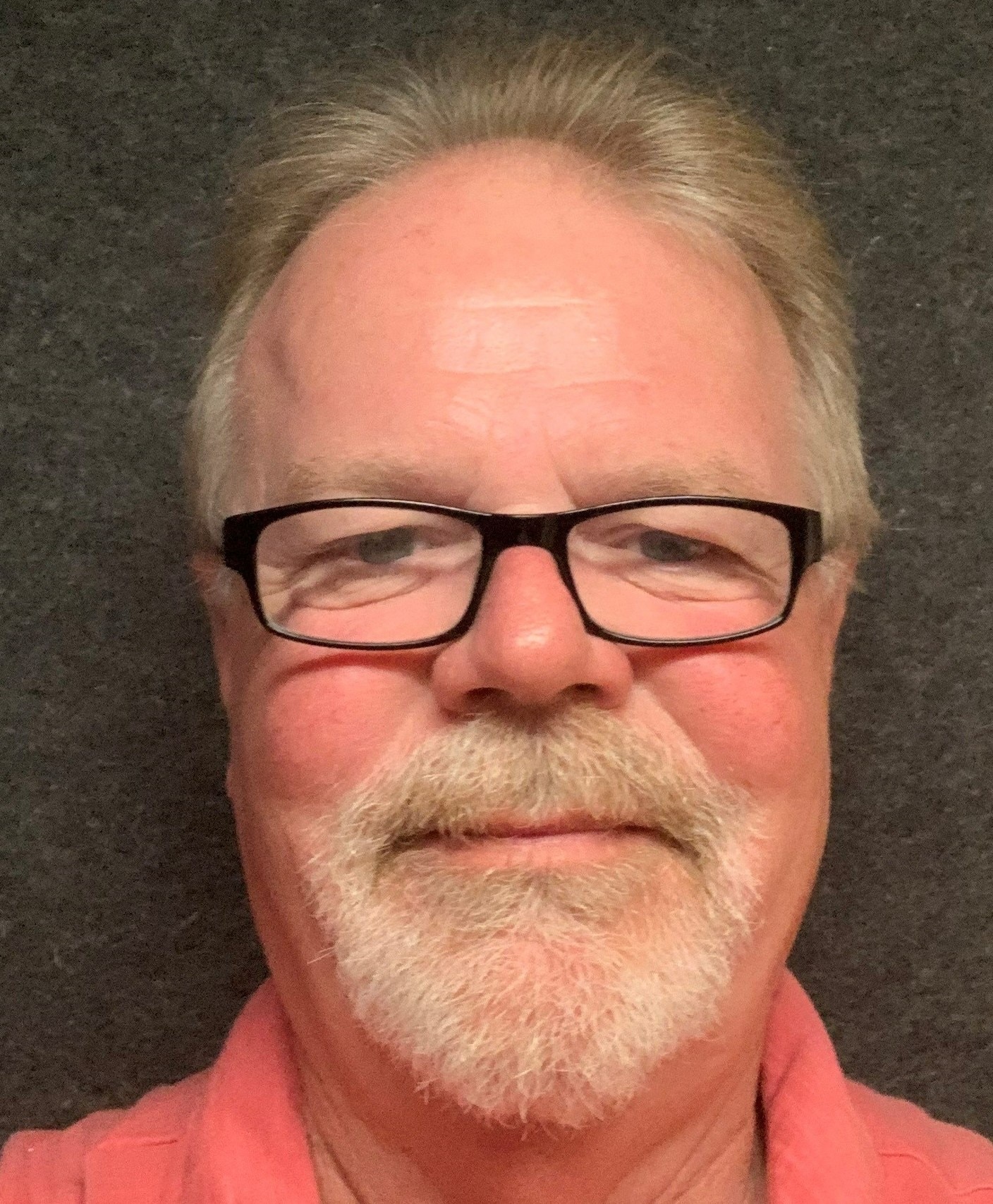
Customer Spotlight
SmartCap is revolutionizing the use of AI in manufacturing with a new 400,000 square foot self-operating factory in Fort Worth, Texas. By utilizing the Internet of Things, the automotive accessory manufacturer achieved a needed competitive edge for the North American market.
Over 20 robots cut, bend, weld and paint metal sheets into component parts for stainless-steel truck caps. These robots are managed by an array of WiFi, sensors and laser beams controlled over a local area network (LAN) to ensure a safe, streamlined working environment.
Automated process adjustments controlled by an AI algorithm have been doubling factory output every few months.
Based in South Africa, SmartCap has already achieved international recognition with their modular canopies and other accessories for pickup truck beds. But as the company sought to grow their U.S. business, they realized they needed to modernize their entire manufacturing process with smart factory technology.
“The only way for us to come here was to automate,” explains Jason Ehrlich, Vice President of Global Marketing, SmartCap.
Charting a path to building a successful smart factory
Satisfying orders from 1,500 authorized SmartCap dealers across North America generates high production demand. The massive size of the plant allows for critical growth opportunities. So does a focus on utilizing AI and IoT.
At the core of the Spectrum Business partnership is a modular platform designed to deliver and manage data across the entire AI operation, Managed Network Edge with WiFi and cameras.
“We needed a team of people to help us build the network that manages the automation and the data it runs on,” says Andrew White, Vice President of Operations, SmartCap.
This technology partnership is further strengthened with the participation of Cisco Meraki, manufacturer of the vital components that make the network run. As a Cisco Gold Certified Partner, Spectrum Business is ideally positioned to help SmartCap design for scalability and sustained success.
Capturing efficiencies across the smart factory floor
The smart factory’s WiFi capacity, supported by employees monitoring the factory floor, is key to maintaining high benchmarks in quality and output.
Overseeing every aspect of operations in and immediately around the plant itself are over three dozen AI-controlled Meraki cameras. They help ensure maximum assembly line efficiency and employee safety.
Ehrlich sees the Managed Network Edge LAN platform as vital to establishing an AI-driven ecosystem where SmartCap can thrive. The platform also monitors and protects the SmartCap factory against cyberattack using a co-managed firewall.
“Obviously, the infrastructure must be in place before anything works in a smart factory,” White notes.
In June 2025 this achievement was recognized when Cisco awarded SmartCap its inaugural Customer Achievement Award in the category of Operations Pioneer.
Scaling for the future
A critical strategic focus of SmartCap is to stay on a fast growth trajectory. The vast size of the Fort Worth factory footprint will enable them to add more features and productivity enhancements as they learn how to do more with their network.
Another way SmartCap focuses on future growth is by investing in scalable infrastructure. This includes the modular nature of the Managed Network Edge platform and the ability to add cameras, access points and switches whenever needed.
“When I started putting this factory together, I thought the infrastructure was going to be the biggest problem,” White says. “To date, it’s been the least.”
Want to learn more about this successful, ongoing partnership? You can read the full case study.
Keep up on the latest
Sign up now to get additional stories on connectivity, security and more.
Forms cannot be submitted at this time. Please call to speak with a representative.